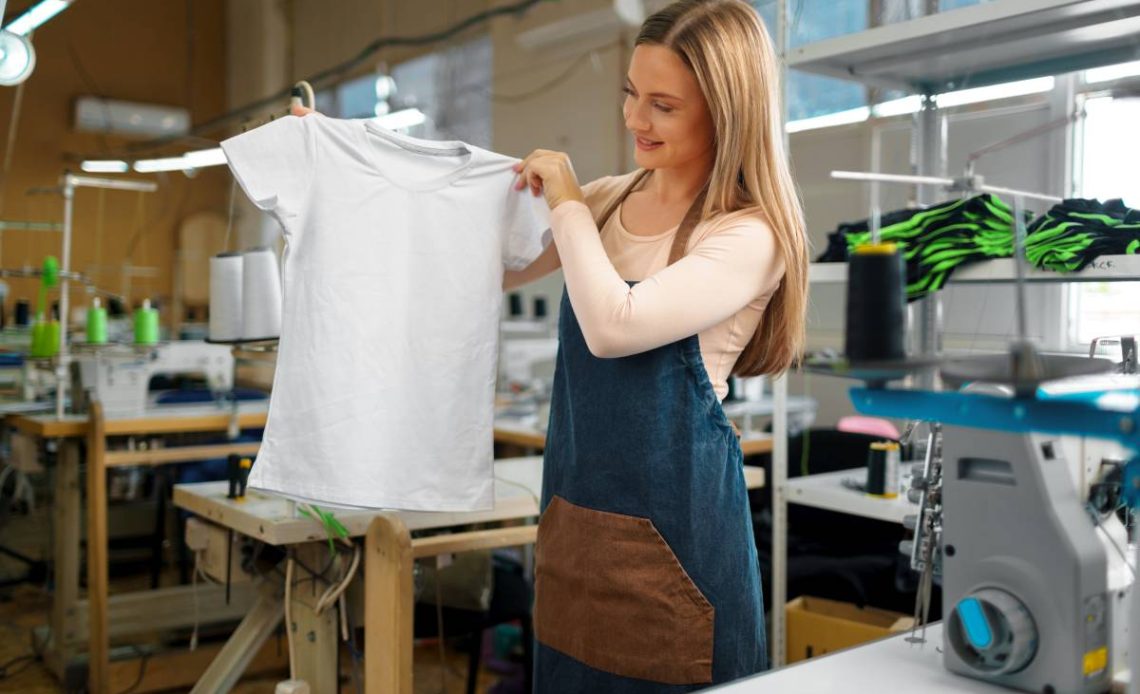
Produkcja koszulek to złożony proces, który wymaga uwzględnienia wielu czynników wpływających na końcową cenę. Niezależnie od tego, czy planujesz rozpocząć własną markę odzieżową, czy po prostu jesteś ciekaw procesu produkcyjnego, zrozumienie struktury kosztów jest kluczowe. W tym artykule szczegółowo przeanalizujemy wszystkie elementy składające się na koszt wyprodukowania koszulki – od wyboru materiałów po końcową kalkulację.
Z czego składa się koszt produkcji koszulki?
Zanim zagłębimy się w szczegóły, warto zrozumieć, że końcowa cena koszulki to suma wielu elementów. Podstawowe składniki to nie tylko materiał i szycie, ale również koszty związane z projektowaniem, transportem czy magazynowaniem. W przypadku produkcji na większą skalę, każdy z tych elementów może znacząco wpłynąć na cenę jednostkową.
Producenci odzieży muszą brać pod uwagę nie tylko bezpośrednie koszty materiałów, ale również wydatki związane z prowadzeniem działalności, takie jak utrzymanie maszyn, wynagrodzenia pracowników czy media. Te wszystkie czynniki składają się na końcową cenę produktu.
Co wpływa na cenę koszulki?
Do wyprodukowania jednej koszulki niezbędne są także akcesoria, takie jak nici, metki czy wszywki. Chociaż pojedynczo są one tanie, przy większej skali produkcji znacząco podnoszą całkowite koszty. Przykładowo, metki z nadrukiem wysokiej jakości kosztują około 1-2 zł za sztukę.
Ile wynosi koszt robocizny przy produkcji koszulek?
Produkcja w Polsce kontra Azji: Decydując o lokalizacji produkcji, warto mieć na uwadze ukryte koszty. Choć niższe stawki za szycie w Azji mogą wydawać się korzystne, często wiążą się z dłuższym czasem realizacji zamówienia, większym minimalnym nakładem oraz wyższymi wydatkami na transport i kontrolę jakości.
Jak wygląda proces produkcyjny i jego koszty?
Proces produkcji koszulki to szereg precyzyjnie zaplanowanych etapów, z których każdy generuje określone koszty. Od momentu projektowania do finalnego pakowania, każdy krok wymaga odpowiednich nakładów finansowych i czasowych.
- Projektowanie i tworzenie szablonów (2-3 dni)
- Zakup i przygotowanie materiałów (3-5 dni)
- Krojenie materiału (1 dzień)
- Szycie elementów (1-2 dni)
- Wykańczanie i kontrola jakości (1 dzień)
- Prasowanie i pakowanie (1 dzień)
Co składa się na poszczególne etapy produkcji?
Każdy etap produkcji wymaga specjalistycznego sprzętu i wykwalifikowanej kadry. Na przykład, profesjonalna maszyna do szycia przemysłowego to wydatek rzędu 5000-15000 złotych, a jej obsługa wymaga doświadczonego pracownika. Do tego dochodzą koszty energii, która przy pełnej linii produkcyjnej może wynosić nawet kilkaset złotych dziennie.
Jakie są dodatkowe koszty w produkcji?
Oprócz podstawowych kosztów materiałów i robocizny, należy uwzględnić wydatki związane z transportem, magazynowaniem oraz marketingiem. Transport materiałów i gotowych produktów może stanowić nawet 10-15% końcowej ceny produktu. Magazynowanie generuje stałe koszty, niezależnie od wielkości produkcji.
W jaki sposób wielkość produkcji oddziałuje na koszty jednostkowe?
Wielkość produkcji odgrywa istotną rolę w kształtowaniu kosztów jednostkowych. Przy większych ilościach zamówień można osiągnąć znaczące oszczędności, które wynikają z korzystniejszych cen materiałów oraz bardziej efektywnego wykorzystania zasobów produkcyjnych.
Jak skutecznie zoptymalizować koszty produkcji?
Proces optymalizacji kosztów rozpoczyna się od ustalenia minimalnej opłacalnej wielkości partii produkcyjnej. Dla większości firm produkcyjnych jest to zazwyczaj zakres 100-200 sztuk, przy którym koszt jednostkowy staje się ekonomicznie uzasadniony. Przy zwiększeniu produkcji do 1000 sztuk można zyskać oszczędności na poziomie 30-40% w porównaniu z niewielkimi seriami.
Jak wygląda końcowa kalkulacja kosztów?
Podsumowując wszystkie składniki, możemy przedstawić przykładową kalkulację dla standardowej koszulki bawełnianej produkowanej w Polsce:
- Materiał podstawowy: 12-15 zł
- Dodatki (nici, metki): 2-3 zł
- Robocizna: 8-12 zł
- Koszty dodatkowe (transport, magazynowanie): 4-6 zł
- Marża producenta: 15-20%
Finalny koszt wyprodukowania jednej koszulki, w zależności od jakości materiałów i skali produkcji, może wahać się od 30 do 60 złotych. Przy większych zamówieniach i optymalizacji procesów produkcyjnych, koszt ten może zostać obniżony nawet o 30%.
Pamiętaj, że przedstawione koszty są orientacyjne i mogą się różnić w zależności od wielu czynników, takich jak lokalizacja produkcji, wybrane materiały czy aktualne ceny na rynku. Dlatego przed rozpoczęciem własnej produkcji warto dokładnie przeanalizować wszystkie składniki kosztów i dostosować je do swojego modelu biznesowego.